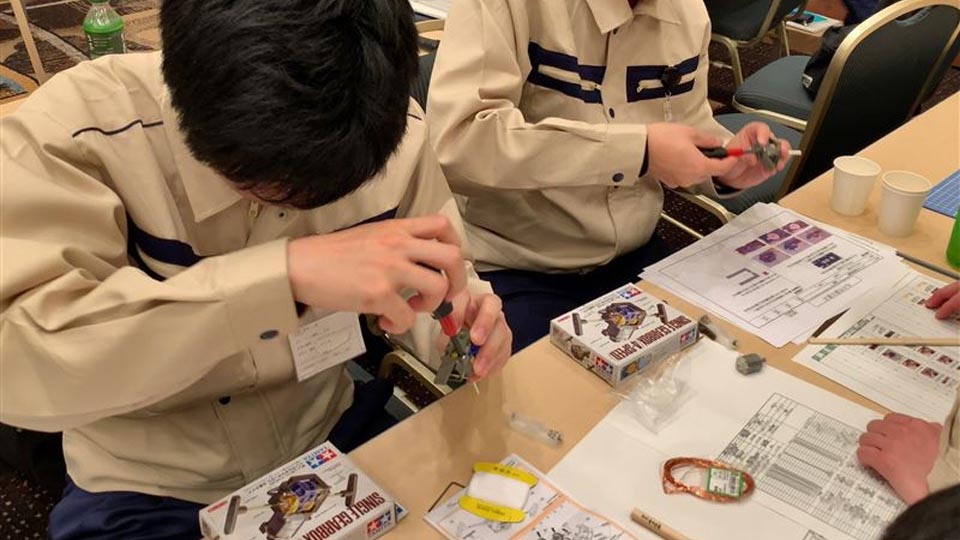
How Do the Japanese Train Their Employees to Be More Effective?
To provide training to a new employee is the very first important step of human resource development of a company. Many companies place importance upon providing a training to their new employees who play an important role in the company in the future. In fact, by providing an intense training course or focusing mainly on stress management may cause the new employees to quit the job very easily. Therefore, the most important thing in providing a training course to the employees is to establish a clear training goal.
Aging population and declining birth rate are the problems that affect the labor force in the market and many inevitable business difficulties while the consumer market is expanding. The problems have caused intense human resource competition due to a great demand of quality employees from the business sector. Thus, the good employee management for mid to long-term future growth of the business is a crucial necessity in the current situation.
The Ministry of Health, Labor and Welfare (MHLW), in cooperation with the Ministry of Education, Culture, Sports, Science and Technology (also known as MEXT) of Japan reported that in Japan, from March 2019, the employment rate of the newly graduated students was as high as 97.6%. Despite a slight decline from 2018, the rate was very high and was expected to remain at this level. However, among these employees, the turnover rate of those after the three years of graduation was as high as 30%, while the turnover rate of senior high school graduate students and junior high school graduate students were at 40% and 60%, respectively.
Researches of Itochu and Toyota Industries Reveals Passing on the Visions is Vital
“3 Principles” of Itochu
Itochu, one of the biggest trading companies in Japan, had performed a new employee training test with a short training camp under the vision of “3 Principles” of Mr. Chubei Itoh, the founder. The “3 Principles” consist of work, colleagues, and workplace which gear the employees’ mindset to be exactly in line with the company’s required direction.
The training performed on 116 salespersons to experience the production base and work with production department throughout the training period, including being volunteers for social responsibility activity within the areas surrounded the production base. The training aimed to create the employees’ understanding of the production process and how each product was developed through processes. As a result, the salespersons would be more responsible in selling more of the company’s products.
Origin of “Automatic System” of Toyota Industries
Since 2007, Toyota Industries has provided training to new employees to work on “Type G automatic loom” model assembly, the origin of the company and it was the idea of Mr. Sakichi Toyoda, the founder.
The Type G automatic loom was developed in 1924 and it has been the foundation of designing and developing the company’s automatic system till today. By trying to assemble the model with their own hands, the employees are well cultivated with the practice of real work according to the typical Toyota Production System. This year, the training will be in September, just like every year.
TDK Underlines Every Step of Learning
TDK’s training course for new employees is a 3-week “production course” in which the new employees will receive the training on designing, material selection, production planning, actual production, quality checking, and selling. The company explained that every process of training is the best way to decrease defects.
In 2018, TDK organized a training course for 144 new employees to produce stopwatches. Groups of 6 employees had to produce the most punctual stopwatch and they had to present in front of all participating employees. The winning team of 2018 designed a stopwatch with LED light that would turn on itself after the 3-minute time passed. It was the most punctual stopwatch with low production cost which could actually be produced. The HR department explained that such learning would help the employee to better understand the production.
Training via VR
KDDI has brought the Virtual Reality (VR) technology to train new employees and interns to learn how to lay the company’s cable under the water. Apart from learning any time from anywhere, it is a cost-saving when compared with the use of robots or submarines to actually examine the cable under the water.
In addition, the company is developing other new applications to enhance VR learning level. According to the company’s explanation, an interesting presentation would make the employees less worried and therefore able to learn more efficiently.
Service Mind Enhancement with Social Responsibility
Joyo Bank trains their new employees through tree growing. In 2019, there were 144 new employees attending tree growing activity in provinces where the branches are located, totalling more than 800 trees.
The tree growing training for the new employees of the bank has been organized since 2014. It aims to create understanding among the employees of how important the environment is and to promote employee’s responsibility which is not limited within their duties to the company but to the society. This will lead to a better service mind.