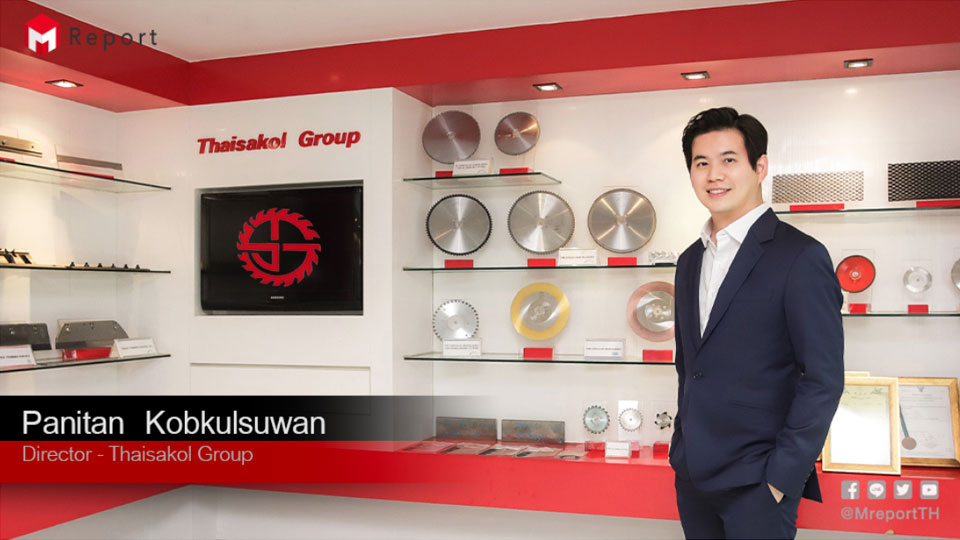
Four decades of ‘Thaisakol Group’ entering the manufacturing transformation
After a four-decade journey, "Thaisakol Group," the company that has been behind the technology of "cutting," a fundamental process that permeates practically every industry, is entering "manufacturing transformation" and launching a new portfolio to suit the needs of the manufacturing industry's future.
Mr. Panitan Kobkulsuwan, Director of Thaisakol Group Company Limited, a group of businesses that specializes in integrated cutting and was founded in the early years of Thai industry in 1975, revealed his opinions in an interview with M Report industry news agency as follows.
Not just a cutting specialist, but manufacturing transformation
"Cutting" is a fundamental process that permeates almost every industry, such as woodworking, metallurgy, paper, pulp, plastic, rubber, electronic components, tools, and equipment, used in more than 40 different types of businesses.
According to Mr. Panitan, the company recently celebrated its 47th anniversary on August 20. Thaisakol Group runs a full-service cutting-edge technology business through its four group firms, including
- Thaisakol Group imports and distributes world-class brand machinery and cutting tools such as circular saw blades, knives, band saw blades, and other related products which are in subtractive manufacturing (SM), or the production of parts by removing the material. It also expands the portfolio to additive manufacturing (AM), which is the production of parts by adding material, also referred to as 3D printing.
- Thaisakol B and B manufactures and processes 100% Japanese technology-based industrial blades under the flagship brand KANEFUSA to support domestic industrial needs and under other brands to support the OEM market.
- Thaisakol Service Center provides high-quality sharpening and repair services for blades, saw blades, and all kinds of cutting tools.
- Thaisakol Machinery provides comprehensive machinery maintenance services and is the location of the Thaisakol Innovative Knowledge Center for Manufacturing Idea (THINK).
Currently, Thaisakol is home to more than 20 world-class brands, including EVERRISING, KANEFUSA, STARK, WIKUS, SOCO, JIH-I, DESKTOP METAL, etc.
As for the primary machinery brand that Thaisakol has imported to market and grow alongside the Thai automotive sector, EVERISING, a saw machine from Taiwan, is one of the world’s top 3 brands of circular saws and band saws that come in all sizes for every industry and can cut all grades of metal including steel, aluminum, and copper, as well as all forms of solid shafts or round and square tubes.
Thaisakol maintains a strong operation even during crises, such as the COVID outbreak over the past two years, thanks to a comprehensive business of cutting technology that is the ideal combination between machinery, a product that grows well during an economic expansion, and cutting tools like blades, which are consumables that are used continuously in any economy.
Additionally, Thaisakol's integrated business operations give it the chance to provide close customer service to clients in a range of industries. It benefits Thaisakol to be very adaptable and able to seize new possibilities and react well to the situation since they can swiftly and thoroughly understand the market conditions.
Technology from world-class brands
Mr. Panitan highlighted that choosing premium brand products to market is one of Thaisakol's capabilities. Along with providing current technology and quality assurance, it also enables Thaisakol to quickly impart knowledge and modern technology to their clients and stay abreast of new developments that can reveal opportunities to grow.
As a result, the company started to broaden its portfolio in 2017 to include the additive manufacturing (AM), commonly known as 3D printing, which will dramatically alter the way we currently manufacture things.
The use of 3D printing will open up new possibilities in manufacturing that weren't previously possible using conventional manufacturing techniques. Additionally, it is conceivable to offer creative manufacturing solutions based on evolving product design imaginations when SM and AM manufacturing methods are combined.
According to Mr. Panitan, the majority of Thai manufacturers are still independent contractors that primarily work for OEMs and compete primarily on price. They are faced with cutting expenses while the selling price rises every year. With new technologies, however, they will be able to develop novel items and have their own brands. For instance, the aluminum buses produced by Sakun C Innovation Company, one of Thaisakol’s clients, is a supplier that supports 3D printing technology.
Metal 3D printing technology may be new in Thailand, but it has actually been around for a while. Despite the fact that it is a technology with numerous benefits, it has not previously been widely used in the manufacturing industry since it is an expensive technology and it takes a long time to make each workpiece.
Thaisakol Group was one of the first businesses to introduce industrial-grade metal 3D printers to the Thai market, and it is now importing 3D printing technology that is fast enough and affordable enough to be used in the manufacturing industry, generating a lot of interest.
The greatest advantage of 3D printing is its capacity to inspire innovative thinking among entrepreneurs and to enable the creation of products from ideas that would otherwise never be realized due to production constraints. Additive manufacturing, or 3D printing, overcomes these constraints as opposed to conventional, process-intensive manufacturing, which requires a lot of time or for which there isn't even a method that can be manufactured.
The capabilities of 3D printing make it a solution to the challenges of producing intricate things. The aerospace and medical sectors are among the first to employ 3D printing technology for items like turbine blades for airplane engines, prosthetic bones, implants, etc.
Today, 3D printing technology is employed in a wide range of industries, including product development and research, which speeds up the development of new inventions.
Additionally, the shift to electric vehicles will provide a wonderful opportunity for 3D printers to respond to attempts to lower the weight of the vehicle by creating EV parts that are distinct from ICE car parts. EV parts are designed with assembly reduction, weight reduction and complex structures.
Thaisakol Group has selected to highlight the most innovative and high-quality goods and services from its additive manufacturing (AM) portfolio, including:
- Desktop Metal is 3D printing technology that covers more than 200 types of materials, including metals, polymers, elastomers, ceramics, composites, and wood.
- BIGREP is a polymer printer with FFF (fused filament fabrication) system that can print large pieces up to 1000x1000x1000 mm.
- DLyte is a dry electropolishing machine.
- Customers can come and experience all these technologies at THINK by THAISAKOL, a 3D printing service center or 3D LAB that will inspire change and revolutionize future manufacturing.
DESKTOP METAL’s Studio System
The Studio System from Desktop Metal brings new capabilities to the world's first office-friendly high-resolution 3D metal printing solution. It is suitable for prototype production jigs, tools, and low volume manufacturing.
The original Studio System consists of 3 parts: a printer, a debinder and a furnace. It supports a wide variety of materials: stainless steel, low-alloy steel, copper, nickel-based superalloy, and tool steel.
The upgraded Studio System 2 is more environmentally friendly since it produces parts without the requirement of debinding process to clean the workpiece after printing by using only the printer and the furnace.
DLyte Electropolishing System
DLyte Electropolishing System is yet another green technology. The rough surface peaks will gradually be removed by electricity flowing through the electrolyte until the surface is glossy and smooth. This method of polishing prevents physical abrasion from occurring on the object, leaving no markings and preserving the work's original shape and fine features without rounding.
DLyte Electropolishing System
DLyte Electropolishing System supports the surface finishing of workpieces that require precise shapes. With a polishing process that is environmentally friendly and reduces the risk of using harmful chemicals, it is suitable for use in all industries, including medical, jewelry and decoration, automotive, aerospace, and other industries.