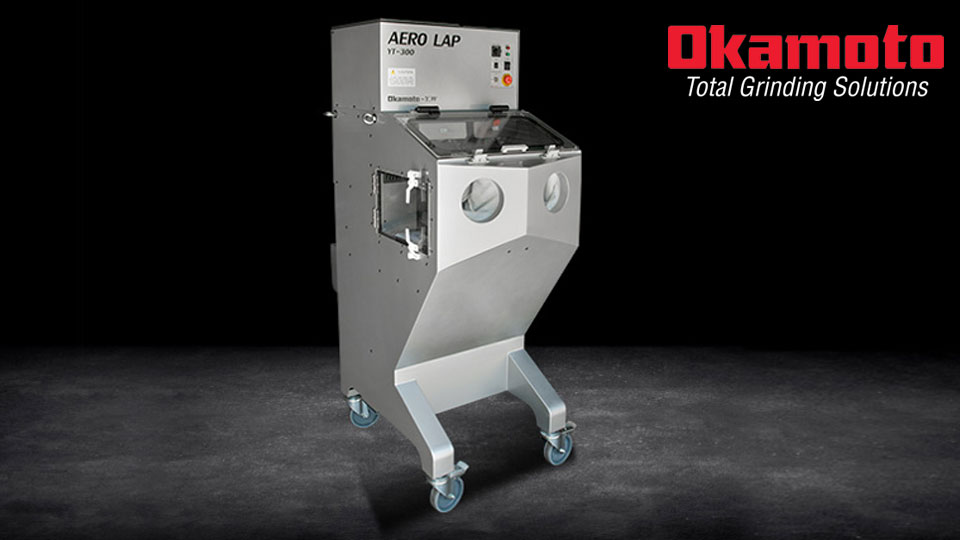
Mirror Finishing Technology for Improvement of Mold Releasability
Press working uses a die for molding is used in various industries because of its high productivity and suitability for mass production. However, molding with a die may make the material difficult to release from the die due to lower releasability and the strong pressure applied to put the material and the die together tightly as well as damage to the molded parts and the die. As such the obstacles, Okamoto has developed the “Aero Lap” method that enables mirror polishing. This article, by Okamoto (Thai) Co., Ltd. joined Yamashita Works Ltd., introduces an outline of the Aero Lap technology, and some examples of actual Aero Lap applications.
1.Introduction
“Plastic working” refers to the working method by which materials, such as metals, are deformed by application of a force to them, and formed into predetermined shapes and sizes by utilizing the property of these materials that remain deformed even after the force is removed (plasticity). Extrusion, rolling, pressing, etc. are classified as plastic working. Among others, press working, which uses a die for molding, is used in various industries because of its high productivity and suitability for mass production.
Molding with a die may make the material difficult to release from the die (due to lower releasability) due to the strong pressure applied to put the material and the die together tightly. As such low releasability reduces productivity due to lost time as well as damage to the molded parts and the die, we generally increase the releasability by applying a special coating and surface treatment to the dies, such as mold release agents, etc.
In collaboration with Professor Koichi Kitajima, Emeritus Professor at Kansai University, our company has developed the “Aero Lap” method that enables mirror polishing, and the “Aero Lap” finish machine that applies the above method (Figure 1). This article introduces an outline of the Aero Lap technology, and some examples of actual Aero Lap applications.
Figure 1: Aero Lap mirror-finishing machine
2.Background of the development
Polishing techniques used for surface modification include “barrel polishing'', by which products are polished by putting them together with media, compounds, water, etc. in a barrel and then rotating and shaking the barrel, and "shot blasting" by which dry abrasive media such as sand or alumina is blasted onto the workpiece. Although barrel polishing has some advantages, such as even complicated shapes that are difficult to polish with a machine can be deburred easily, it makes the corners of the workpiece round, and causes slight dents called “barrel marks”, as well as makes measurement of the surface roughness difficult during the polishing process. However, shot blasting achieves a high quality polishing capability, but tends to cause deterioration in surface roughness, scratches, chipping, etc. due to the frictional heat and impingement heat that arise during the polishing process.
In 1986, when our company was founded, we handled buffing of dies on a contract basis as the process before coating the dies. For the buffing process, various abrasives are applied to the surface of a polishing wheel (buffer) which is made of cloth etc., and the wheel rotates to polish the material. However, buffing has problems, such as finishing the work requires special skills, and workers engaged in buffing cannot not be retained due to the heavy workload.
In order to solve these problems, our company developed the "Aero Lap” blasting technology method.
3.Overview of the Aero Lap technology
“Aero Lap” technology refers to the method that uses the Aero Lap machine, which is similar to a shot blasting machine, a moisture-containing polishing medium called Multi Cones, and an aqueous solution with a rustproof and moisturizing effect specifically used with the Multi Cones.
The Aero Lap machine is a device based on the shot blasting method, which specializes in efficient projection of Multi Cones.
3-1 Overview of the Aero Lap technology
An overview of the Aero Lap technology is illustrated in Figure 2. If Multi Cones, in which abrasive grains and diamonds are combined with an aqueous solution, are irradiated onto a die with an air nozzle, the Multi Cones slide on the die’s surface at high speed. Then, the frictional force generated by such sliding polishes the surface of the die.
Figure 2
In consideration of recent environmental regulations, resource protection, maintenance and the working environment, water diluted with multiple solutions is used to apply the Multi Cones. If Multi Cones with elasticity are projected onto a workpiece by the Aero Lap machine, the Multi Cones generate elastic deformation when they collide with the workpiece, and they convert the projection speed into a frictional force that causes friction on the surface of the workpiece. Mirror finishing and deburring are performed by such frictional action.
This process performs mirror finishing by means of polishing by abrasive grains, moisture, and the projection speed on the viscoelastic core surface combined with the frictional force converted from elastic deformation that is generated when the Multi Cones collide with the workpiece. Figure 3 illustrates the comparison between the conventional method by which dry media is projected, such as shot blasting, with the Aero Lap method. In the polishing work where dry media is used, a satin-like pattern is formed on the surface, because the projectiles collide with only one point on the metal surface. Meanwhile, in the Aero Lap technology, which is a wet-type technology, a smooth mirror finish can be achieved because the projected material slides across the metal surface, whereby the polishing force is not concentrated at one point. In addition, by using projectiles containing an aqueous solution, the frictional heat and impingement heat generated during the polishing process are suppressed by the heat lost through vaporization, and the properties of the metal surface are preserved.
Figure 3: Schematic diagram of the Aero Lap method
3-2 Examples of surface finishing
Figure 4 shows an example of the effect of the Aero Lap technology on a coated surface. In this example, the die surface was polished with the mirror finishing machine (YT-300) for 30 seconds after applying the TiN coating. While surface roughness before the polishing process (Figure 4, left) was Ra=0.195㎛, surface roughness after the polishing process (Figure 4, right) was Ra=0.038㎛, which is about 1/5 of surface roughness before the polishing process, resulting in a higher sliding capability and improved workpiece releasability.
Figure 4
Figure 5 shows an example of polishing on an ultra-high precision die. The Aero Lap method achieved a mirror-finished surface of Ry=0.3 ㎛, while the surface after profile working was Ry=appx. 1 ㎛.
Figure 5
4. Actual examples of polishing work by the Aero Lap method
The actual examples of polishing work by the Aero Lap method are shown below.
4-1 Deburring of a die
If burrs remain in the die, these burrs will peel off during the production process, and the quality of the product is impaired by such peeled burrs. Therefore, we tested deburring and edge finishing of the die by the Aero Lap method.
A workpiece was prepared by conducting a vacuum heat treatment on a hot-work steel SKD-61 tool with a diameter of φ15 mm and a total length of 20 mm with hardness of HRC55.0, and burrs were formed on the end face of the workpiece with a machining center. Then, the deburring and edge finishing test was conducted by the Aero Lap method. The abrasive used for this code was # 3000 and the polishing time 3 seconds. All the burrs were finished by the Aero Lap method, and the edge quality was maintained.
4-2 Improvement of the polishing quality by adjusting the moisture content
By adding an appropriate amount of water, Multi Cones generate viscoelasticity. In lapping work, Multi Cones projected at 108.0 to 115.9㎞/h, are elastically deformed by collision with the workpiece during the polishing process, and this projection is converted into a frictional force. Multi Cones use the contained moisture to polish the workpiece, and the moisture evaporates at the same time.
As a result of the test on how the moisture content of the Multi Cones affects the polishing work, it was confirmed that water is an effective element for polishing, and it was found that mirror finishing can be achieved at a moisture content of 17 to 30% (Figures 6 and 7).
Figure 6: Appearances of Multi Cones with different moisture content
Figure 7: Results of polishing with Multi Cones with differences moisture content
It was also confirmed that polishing by Multi Cones with a reduced moisture content is still effective in improving surface roughness, although a mirror finish effect cannot be expected.
Although mirror finishing performance depends on the compatibility between the Multi Cones and the workpiece, if you intend to perform mirror finishing, it is it is preferable to control the moisture content of the Multi Cones within 17 to 30%, and maintain the moisture content at 17% or more if you want to maintain the appearance quality of the workpiece.
It was found that water is a necessary element for mirror finishing and improvement of surface roughness by the Aero Lap method combined with Multi Cones. Meanwhile, since the Multi Cones evaporate the moisture during polishing process, the moisture content decreases in proportion to the working time. As the polishing quality is maintained by controlling the moisture content, we have developed an “automatic hydration machine'' that replenishes the water to make up for the moisture that has evaporated by frictional heat in order to maintain the optimal moisture content, and this ensures fine deburring for a long time, and improvement of edge quality.
4-3 Application to medical sheets and pestles
Making use of the Aero Lap method, we developed a three-dimensional PTP sheet (press through pack: a type of package from which tablets and capsules can be pressed out) in 2010 (Figure 8). We developed a three-dimensional PTP sheet by shaping the conventional flat PTP into a triangular prism with its pocket parts outside, so that the tablets can be extracted with one hand, for the purpose of preventing accidental ingestion by elderly people, etc., and proposed this sheet for use in the medical field. The sheet is polished by the Aero Lap technology to enhance its releasability.
Figure 8: Newly-designed three-dimensional PTP sheet from which tablets can be removed with one hand
In addition, we improved the releasability of the metallographic structure of "DSA", a new material that has both the corrosion resistance of austenitic stainless steel and the high hardness of martensitic stainless steel by applying Aero Lap finishing to the "tableting pestle", the die used to shape tablets for medical purposes. Although high-hardness stainless steel generally increases the difficulty of machining due to its hardness and toughness, the Aero Lap technology can solve this problem and achieve a stable supply of tableting pestles that do not require plating (Figure 9).
Figure 9: Example of a mirror-finished surface using the Aero Lap method for the purpose of improvement of the releasability of the tableting pestle (left: pestle finished by the Aero Lap method, right: unfinished pestle)
5. Conclusion
This article introduces the surface finishing technology for dies using the “Aero Lap” method. Polishing with Aero Lap technology enables mirror-finish quality for the complex shape of dies and cutting tools in a short time. Last year, our company developed a mirror-polishing machine equipped with a robot, in order to automate the Aero Lap method (Figure 10). This method eliminates the risk of leaking of the abrasive material to the outside by performing the series of operations related to mirror-finish work within the machine, as well as ensuring safety by automation. We will continue to improve and update the efficiency of our finishing technology in order to contribute to the improvement of on-site productivity.
Figure 10: Mirror-polishing machine equipped with a robot
Interested please contact:
Okamoto (Thai) Co., Ltd.
174 Mu2, T.Chamaeb, A.Wangnoi, Ayutthaya 13170
Tel. 035-958-499 (automatic)
Email : [email protected]
Website : www.okamotothai.com