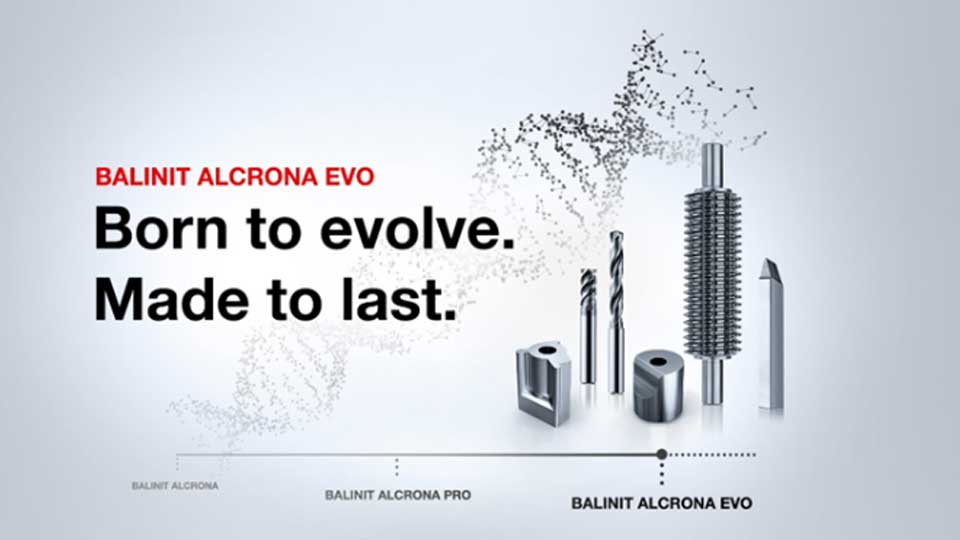
The new generation of a globally established universal coating: Oerlikon Balzers presents BALINIT ALCRONA EVO
Introducing BALINIT ALCRONA EVO, Oerlikon's third-generation PVD coating. It offers over 30% longer tool service life compared to its predecessor. This enhancement significantly improves manufacturing efficiency for customers in the metalworking industry.
Balzers, Liechtenstein, February 29, 2024 – When BALINIT ALCRONA was launched in 2004, Oerlikon Balzers introduced a universal coating for gear cutting, milling, stamping and forming that allowed customers in the metalworking industry to significantly improve their production performance. With BALINIT ALCRONA EVO, Oerlikon’s technology brand for thin film surface solutions is now introducing the third generation of the PVD coating. Extensive enhancements mean the service life of tools with BALINIT ALCRONA EVO can be more than 30 percent longer than with its predecessor coating. The optimized wear resistance of BALINIT ALRCONA EVO also reduces the regrinding stock volume when reconditioning, which increases the number of regrinding cycles per tool. This saves valuable resources and customers can significantly reduce the cost of new tools.
The slogan “Born to evolve. Made to last.” for BALINIT ALCRONA EVO reflects the history of this successful all-round coating. Since its introduction 20 years ago, Oerlikon Balzers’ surface experts have continuously developed and refined the coating composition to meet customers’ ever-increasing demands for even longer tool service life.
Major enhancements produce more than 30 percent better performance than previous coating
In addition to high-quality products, maximizing tool life is critical in order to reduce tool costs and achieve cost-effective production in the metalworking industry. BALINIT ALCRONA EVO offers more than 30 percent better performance than its predecessor BALINIT ALCRONA PRO.
Important properties of the PVD coating have been optimized to ensure outstanding performance: BALINIT ALCRONA EVO is even harder, making it more resistant to abrasive wear, while its resistance to adhesive wear has also been increased. In addition, the enhanced toughness benefits tool performance in metal forming, and especially in machining applications such as gear cutting and wet milling. Its lower thermal conductivity minimizes crater wear on HSS tools, and thanks to the reduced compressive stress of BALINIT ALCRONA EVO, the coating adheres even better to the tool during use. Only the light gray coating color and the range of coating thicknesses remain unchanged.
BALINIT ALCRONA EVO has already produced impressive results in a test carried out by a Tier 1 supplier in the automotive industry. In dry machining with an HSS hob, it increased the tool service life by more than 40 percent compared to its predecessor. The improved performance of BALINIT ALCRONA EVO allows users to further increase their cutting parameters in order to reduce machining times and thus overall production costs. Extending the tool service life also keeps the number of tool changes and associated downtime to a minimum, resulting in lower overall energy consumption.
Sustainable production: reconditioning without loss of performance saves tool costs
Regrinding and recoating make a valuable contribution to environmental protection while offering almost the same quality and potential performance as the original coating. In addition to improving the environmental footprint, reconditioning reduces the cost of purchasing new tools by about 23%. The improved performance and reduced wear also reduce regrinding stock volume and extend the number of regrinding cycles per tool. This is all part of Oerlikon’s consistent strategy of being a sustainable and resource-efficient supplier to the metalworking industry.
Available at all customer centers worldwide
Dr. Andreas Reiter, Head of Product Line Tools, explains: “20 years ago we launched BALINIT ALCRONA, a new generation of AlCrN-based PVD coatings. The next development, BALINIT ALCRONA PRO, significantly improved performance in machining and forming for our customers. BALINIT ALCRONA EVO is another milestone in the evolution of this versatile coating. It’s already available in all our global customer centers in more than 30 countries in Europe, North and South America and Asia, so our customers can now benefit from even better performance and longer tool service life.”
For more information, companies can contact their local customer center representative:
https://www.oerlikon.com/balzers/global/en/infopoint/worldwide/
Further information and test results with BALINIT ALCRONA EVO can be found at:
www.oerlikon.com/balzers/balinit-alcrona-evo
The evolution of a globally established PVD coating for numerous applications in the metalworking industry: the latest development, BALINIT ALCRONA EVO, offers more than 30 percent better performance than its predecessor. Image: Oerlikon Balzers
BALINIT ALCRONA EVO is the ideal universal coating for a wide range of applications in the metalworking industry, such as gear cutting and end milling. Image: Oerlikon Balzers
With BALINIT ALCRONA EVO, customers in the stamping and forming industry benefit from longer tool service life and high-quality products. Image: Oerlikon Balzers
BALINIT ALCRONA EVO has already demonstrated its capabilities in a test conducted by a Tier 1 automotive supplier for gear hobbing, increasing tool service life by more than 40 percent. Image: AdobeStock
For further information, please contact:
Petra Ammann
Head of Marketing Communications
Oerlikon Surface Solutions
T +423 388 7500
[email protected]
http://www.oerlikon.com/
About the Oerlikon Surface Solutions Division
Oerlikon is a leading global provider of surface and additive manufacturing solutions and services. The division offers an extensive portfolio of market-leading thin-film, thermal spray and additive manufacturing technologies, equipment, components and materials. Emission reduction in transportation, maximized longevity and performance of tools and components, increased efficiency and intelligent materials are hallmarks of its leadership. Pioneering technology for decades, the division serves customers with standardized and customized solutions across a worldwide network of more than 170 sites in 37 countries.
With its technology brands – Oerlikon Balzers, Oerlikon Metco and Oerlikon AM – the Oerlikon Surface Solutions division focuses on technologies and services that improve and maximize performance, function, design, reliability and sustainability, which are innovative, game-changing advantages for customers in the automotive, aviation, tooling and general industries and in the luxury, medical, semiconductors, power generation and oil & gas markets.
The division is part of the publicly listed Oerlikon Group (SIX: OERL), headquartered in Switzerland, which has more than 12 600 employees and generated CHF 2.7 billion in revenue in 2023.
For more information see: www.oerlikon.com/surface-solutions