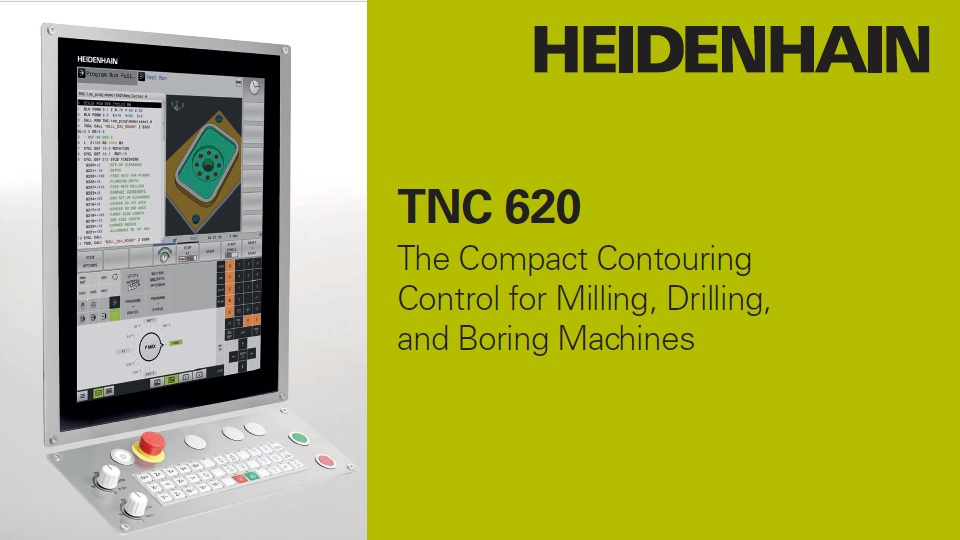
TNC 620 – The Right Control for Milling, Drilling and Boring Machines
TNC 620 is compact and easy to read. The TNC 620 is a compact but versatile contouring control for up to five controlled axes. Thanks to its flexible operating concept-workshop-oriented programmability with HEIDENHAIN conversational programming or offline programming and its scope of features, it is especially suited for use on universal milling, drilling and boring machines for the following:
- Series and single-part production
- Toolmaking Machine building
- Research and development
- Prototypes and pilot plants
- Repair departments
- Training and education facilities
Multitouch operation
The TNC 620 is available not only in the conventional version with a standard screen and keyboard, but also with a touchscreen and keyboard. Whether zooming with two fingers, rotating, or moving, you operate the TNC 620 quickly and easily with your fingertips.
And it offers more features as that necessary and helpful
Free contour programming (option 19)
Not all workpieces are dimensioned for conventional NC programming. Thanks to FK, the control’s free contour programming feature, in such cases you simply type in the known data - without first having to convert or calculate it! It does not matter if individual contour elements are not completely defined as long as the complete contour has been. If the given data results in more than one mathematical solution, the helpful TNC 620 programming graphics show you the possible variants for your selection.
Milling cycles for complex contours, cycles for drilling, boring and spindle alignment, cycles for linear and circular point patterns
Comprehensive fixed cycles for milling, drilling, and boring
Frequently recurring operations that comprise several working steps are stored in the TNC 620 memory as standard cycles. You program them under conversational guidance and are supported by graphics that clearly illustrate the required input parameters.
Standard cycles and cycles for complex contour (option 19)
In addition to the fixed cycles for drilling and tapping (with or without floating tap holder), optional cycles (option 19) are available for thread milling, reaming, engraving, and boring, as well as drilling patterns, milling cycles for face milling flat surfaces, for clearing and finishing pockets, slots, and studs. The TNC 620 maintains a finishing allowance on the wall and floor surfaces during roughing. When roughing with different tools, the control identifies material remaining in inside corners so that it can be cleared later with smaller tools. A separate cycle is used for milling to the finished dimensions.
Fast pre-setting with HEIDENHAIN touch probes
Workpiece touch probes from HEIDENHAIN help you to reduce costs in the workshop and in series production: together with the TNC 620’s cycles, touch probes can automatically perform setup, measuring, and inspection functions.
Five-axis machining with swivel head and rotary table
When you are programming away from the machine, the TNC 620 automatically takes the machine geometry into account
Tilting the working plane
Tilting the working plane (option 8) Programs for contours and holes on inclined surfaces are often very complex and require time-consuming computing and programming work. Here the TNC 620 helps you to save a great deal of programming time. You program the machining operation as usual in the main plane—for example, in X/Y. The machine then runs the program in a plane that has been tilted by one or more rotary axes with respect to the main plane.
Cylindrical surface machining
Cylinder surface machining* (option 8) With the TNC 620 it is quite easy to program contours (consisting of straight lines and arcs) on cylindrical surfaces using rotary and tilting tables: you simply program the contour in a plane as if the cylinder surface were unrolled. You enter a contour in two dimensions—as if in a plane—and the TNC 620 then calculates and machines the corresponding cylindrical contour. The TNC 620 features four cycles for cylindrical surface machining:
- Slot milling (the slot width is the same as the tool diameter)
- Guide-groove milling (the slot width is greater than the tool diameter)
- Ridge milling
- Outside contour milling
Fast execution through short block processing times
The fast block-processing time of maximum 1.5 ms enables the TNC 620 to run fast advance calculations in order to optimally use the dynamic parameters of the machine. In this way, functions like Advance Dynamic Precision (ADP) and look-ahead not only provide very high contour accuracy and surface definition—they also optimize the machining time.
Specification
This is the only example of all TNC 640 functions. For more information please follow the link
https://www.heidenhain.de/de_EN/products/cnc-controls/tnc-620/