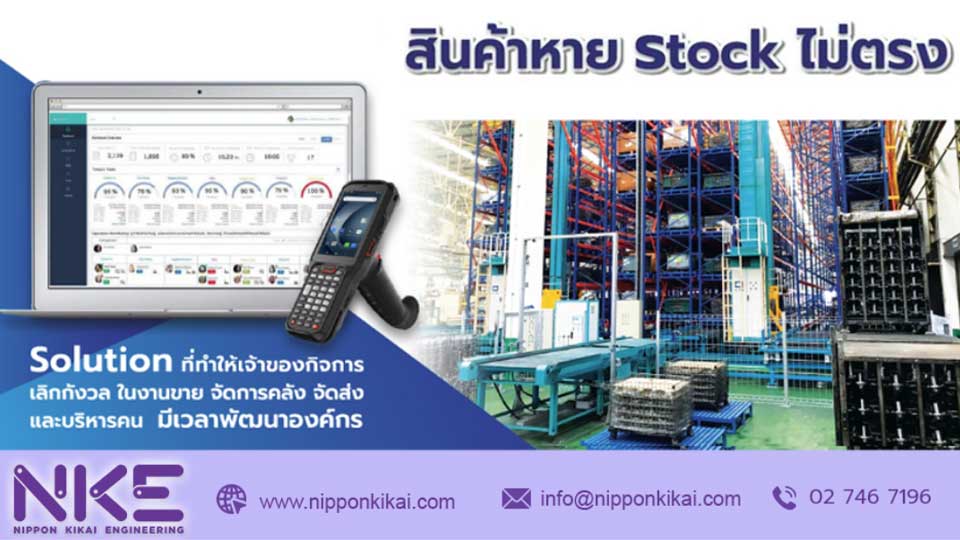
What is AS/RS?
Getting to know AS/RS and example of companies using AS/RS
AS/RS stands for automated storage/retrieval system, which is an automated system that stores and retrieves parts and items to make warehouse management the most efficient.
AS/RS typically stores and retrieves goods at designated locations. It is controlled by the inventory management program to perform a search function, specify a schedule for placing and retrieving goods, and then automatically pick up or store the goods to the destination.
The AS/RS main components consist of
1. AS/RS Racking is a steel structure that is divided into horizontal storage compartments and stacked in layers vertically.
2. A storage/retrieval machine can move both horizontally and vertically to bring products in and out of the racks.
3. Pallets, trays, or storage modules are moved with the goods or stored on the rack in accordance with the storing or pick-up order.
4. A pickup and deposit station is a base station for storing and retrieving goods.
5. Management and control software includes warehouse management software (WMS) and machine management software (WCS).
6. Other devices, such as conveyors and automated guided vehicles (AGVs), are often included as part of the AS/RS.
How to choose AS/RS?
AS/RS enables businesses that deal with order processing and warehousing to automate inventory management with high accuracy and efficiency, especially those with high order volumes, a wide variety of products, a high per piece value, and products stored in challenging temperatures such as freezing temperatures. These factors make AS/RS almost the only viable option.
The AS/RS solutions that are commercially available can accommodate a variety of inventory types, quantities, and speeds. To ensure efficient product management, the distributor will design and customize the system until it is a solution that meets the needs and environment of each customer.
Therefore, the experience of the system distributor is important. If the design team is knowledgeable about the product type and the job characteristics similar to or close to the needs of the customer, they can reduce design risks, recommend good equipment selection, and provide advice to customers. Most importantly, they will provide service at a reasonable cost and complete the job quickly and without trial and error.
AS/RS systems can be categorized as:
- Unit load AS/RS stores and retrieves heavy goods on pallets into racking by moving pallets, or unit loads. This system makes the best use of both horizontal and vertical space. It is suitable for high-volume loading and unloading of goods, and the area has a height of up to 20-50 meters.
- Mini-load AS/RS functions similarly to the unit load AS/RS, but is typically used for smaller, lighter products or workpieces.
- Vertical Lift Modules (VLMs) are two-column storage and retrieval systems with front and back columns. In the center, there is an automated inserter/extractor that stores and retrieves requested product trays.
- Shuttles are automated storage systems that handle pallets, crates, and other items. They are commonly used in general warehouses and factories.
- Horizontal Carousels are horizontally moving handling devices that are suitable for picking up small items.
- Vertical carousels are vertically moving handling devices. They are used to store and retrieve items from high, bulky shelves.
Pros and Cons of AS/RS
Overall, the benefits of AS/RS include reduced labor requirements and space savings in the warehouse. However, how much reduction is possible depends on product type, storage, labor rates, and so on. Even if warehouses are not fully automated, AS/RS can help reduce the burden of repetitive work on workers and make it safer.
However, AS/RS has some drawbacks. To begin, the system incurs design, equipment, and installation costs. Although many studies indicate that it is cost-effective in the long run, it is not suitable for every business, particularly those that want to see a quick return of their investments. In addition, there are maintenance costs. It is also not the right solution for storing and retrieving non-fixed products.
Examples of AS/RS application
Whether or not AS/RS makes sense for your company must be carefully considered. The Material Handling Institute of America (MHI), a non-profit trade association that represents the material handling, logistics, and supply chain industries in the United States, has gathered some interesting case studies for implementing AS/RS:
Reduced walk time equals more orders handling
Park Industries, a US manufacturer of Precisions parts, needs to ship over 5,000 different products every day. As a result, a highly accurate and efficient warehouse system is required.
Initially, the company chose to use two high-speed elevator automatic storage systems to maximize vertical space before expanding to four systems over the next two years, allowing the warehouse to support twice as many products while also allowing for more orders. This is due to the fact that it can reduce the amount of time employees must walk to pick up products. It also connects the system to the ERP for more accurate product data recording.
Vertical storage of medical devices
KLS Martin, a medical device company, decided to use a vertical storage system to make the most of the warehouse's height in order to save space and protect medical devices from dust and chemical contamination, which are common in low-lying areas.
The company also chose to use a variety of software for picking management that operates both from the front of the warehouse and via mobile phones because of a wide range of medical devices, particularly bone and dental implants, and the need to avoid errors as much as possible.
From retrieving volumes to mixed systems
The Kubota Canada warehouse stored more than 78,000 SKUs. Originally, it was divided into two areas: a mezzanine for manual picking and a hi-bay for using transfer trucks. It was discovered to be ineffective and a burden on employees. Furthermore, some products were only shipped out of the warehouse once a year.
As a result, the company renovated the warehouse using the pick and pass concept, dividing the picking area into three sections, two of which use automation systems. Six horizontal carousel modules (HCMs) are used for products that need to be in and out quickly, and four vertical lift modules (VLMs) are used for products that need to be in and out secondarily quickly, while slow incoming and outgoing goods are kept in high storage.
When an ice cream maker ran out of space in freezer
An Alabama ice cream maker experienced insufficient storage space due to the inability to expand the warehouse to keep up with the company's growth, resulting in no space in the freezer for 3,000 pallets.
As a result, the company began storing products vertically and connecting the production line to an AS/RS system 400 feet away using a conveyor belt and labeler. A forklift was initially used to lift the tray into the freezer before switching to two automatic cranes (storage retrieval machines: S/RM) to save space and clearly separate the workspace and storage space.