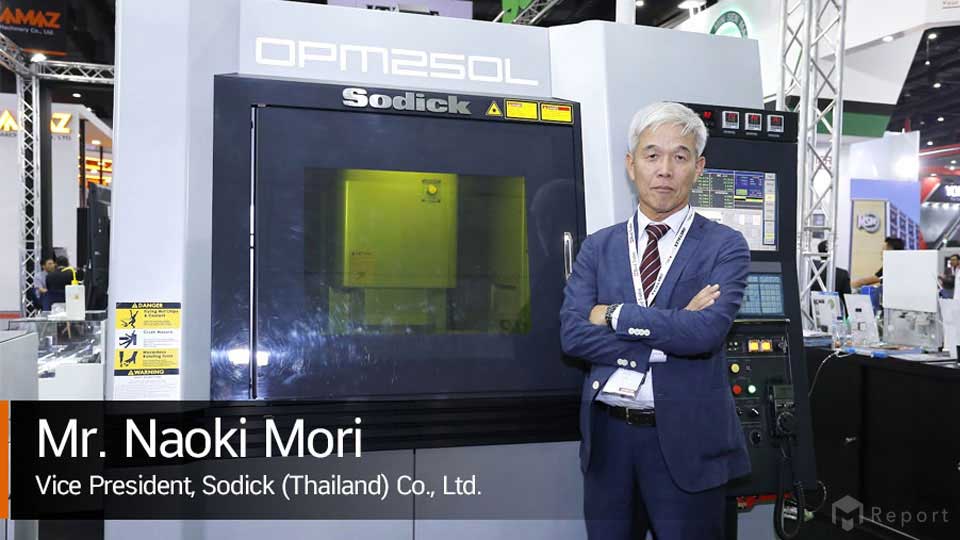
Sodick “OPM250L” Metal 3D Printer Breaks All Rules of Complex Molds Production
Mold with complex shapes and structures makes the work of designing and manufacturing difficult and time consuming. These limitations have been pushing for technological innovations that will increase the alternatives. The Sodick "OPM250L" Metal 3D Printer, a high-precision 3D metal printer in one of the "OPM Series," has changed the way of mold production. Combined with the progress of additive manufacturing and high-speed milling, the OPM series allows one-stop solutions of mold production by forming metal powder into a single metal mold that supports complex shapes and structures without limits. It is suitable for the production of plastic mold, metal casting mold, medical tools, machine parts, and jewelry. In addition, the mold can be produced in a short period of time. Mr. Naoki Mori, Vice President of Sodick (Thailand) Co., Ltd. gave an interview about "OPM250L" that was the highlight of Sodick booth at METALEX 2019 held at the end of last year.
Technology of Metal 3D Printer from Sodick
The success of Metal 3D Printer that is invented and developed by Sodick stems from the combination of laser metal sintering technology that uses 500 watts fiber laser and high-speed milling in the same machine under the concept of "OPM: One Process Machines" focusing on reliability and precision. This allows the user to have the whole process of producing a mold within one machine. Currently, the OPM series is used extensively in the production of one-piece metal molds, especially molds that are highly complex and require a fine surface finish such as molds for printer cartridges. In this Industrial 4.0 era, the OPM250L also supports IoT systems and remote operation.
Mr. Naoki Mori commented, "Combining multiple processes into one machine will help reduce cycle time and reduce the number of mold parts efficiently. It also greatly facilitates mold design and enables production of molds that are structurally too complex to be produced from general cutting tools."