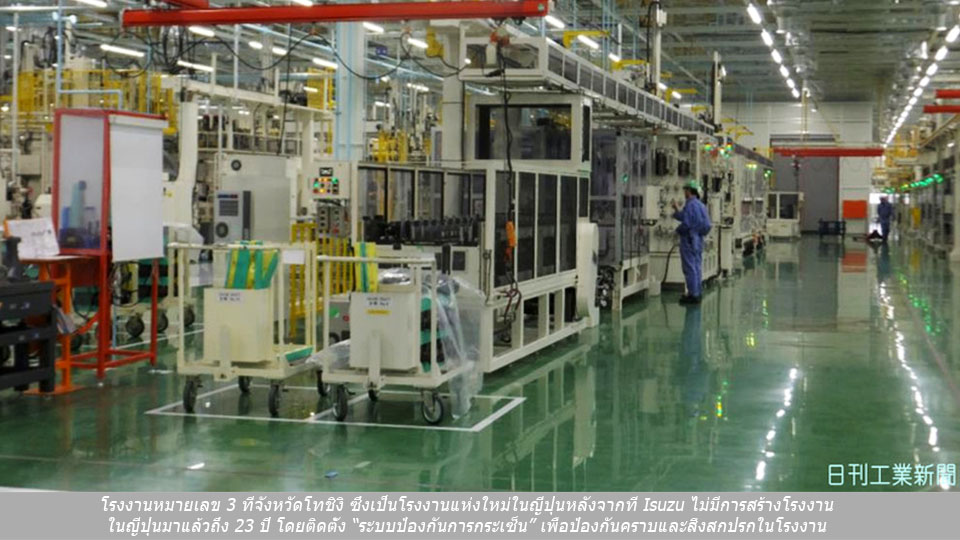
Isuzu Aims to Develop Factories in Japan to Be Smart Factories with IoT
Nowadays, Japanese commercial vehicle manufacturers are actively developing smart factories by using Internet of Things (IoT). Compared to passenger cars, the production of commercial vehicles requires a small varieties of parts with higher durability. Increasing the efficiency of the cooperation between workers and systems has become an important factor. Many companies has quickly adopted new technologies in the production process. Meanwhile, reducing the worker’s workload is also important. Since IoT technology can do both, it has been very well in focus.
Isuzu is also on this trend by developing its Factory no. 3, the latest factory located in Tochigi, to be a smart factory. Currently, the factory is assigned to produce engines for small truck “Elf” released in March, and it complies with the exhaust gas regulations 2016. Building this factory is a positive sign for the industry since Isuzu had not built a single factory in Japan for 23 years.
Mr. Masayuki Murata, the director of Tochigi plant, talked about the new factory as “having more safety than the other factories in the past by utilizing digital technology. It is also a smart factory that is environmentally friendly.” It is a factory integrated with both domestic and abroad bodies of knowledge on manufacturing.
In the engine assembly process, the system was designed to be the database of the parts used along with the assembly instructions. It connects to the network to assign the finished engine a serial number, link it to the parts used in the engine, of which number identifies its original production machines, enabling the traceability. The director Murata added that “With IoT, we can quickly detect and solve a problem and cut the losses by half.”
In addition, IoT leads to increasing the value of products. Commercial vehicles are “working cars that are used daily.” By increasing the production efficiency, the company can position its production as more distinctive than others in the industry. Isuzu has a plan to launch “MIMAMORI” service--a telematics service that analyzes operation information of vehicles remotely. In the future, it will be developed to store information about the parts needed for the vehicle’s repairs, which would save the maintenance time. In other words, the vehicle would have higher uptime.
As for reducing workload, Isuzu installed a “splash guard system” onto the production lines to prevent the lubing oil during cutting process from splashing, which therefore keeps the factory clean. In addition, it adopted a low floor conveyor, eliminating the need of steps or climbing stairs, which means reducing the workload of workers.
The director Murata said that by adopting the IoT system, Isuzu could compress up to two-thirds of conventional personnel. However, there are some situations which could not be solved despite of more workforce. Smart factory plays an important role in administrative management to optimize the personnel.