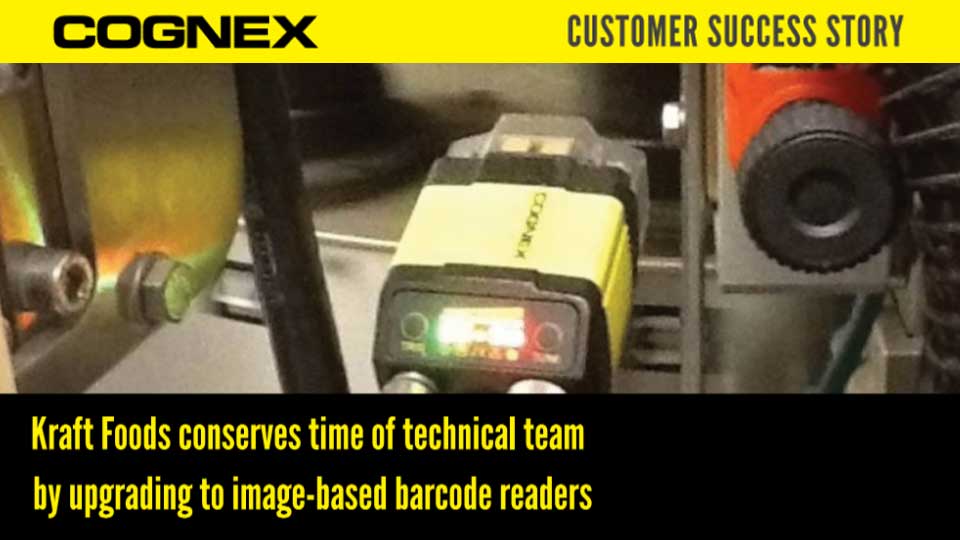
Kraft Foods conserves time of technical team by upgrading to image-based barcode readers
DataMan® barcode readers from Cognex can read any label within a five inch by five inch field of view without requiring adjustment. So the technical staff has been freed from managing the product changeovers.
Allergen management is playing an increasingly important role in the packaged foods industry. Manufacturers are taking better care to avoid labeling mix-ups that sometimes lead to expensive recalls and potential liability concerns.
In order to address these matters, Kraft Foods Canada scans each label after it has been affixed on the packaging line to ensure that it matches the package contents. The laser scanners used in the past to inspect the company’s barbeque sauce products were subject to read failures, especially when changing over to a new product with the label in a different location. A technician had to rush to the line to adjust the position of the barcode scanner to re-center the new label into the path of the laser or the scanner would produce a lot of no-reads.
Kraft solved the problem by switching to Cognex image-based DataMan® barcode readers that can read any label within their five inch by five inch field of view without requiring adjustment. “The outstanding performance of the DataMan 300 barcode readers saves the technical team a considerable amount of time while protecting customers by ensuring the accuracy of our labels,” said Dave Fortin, Technician for Kraft Foods Canada, Saint-Laurent, Québec.
Kraft Foods produces biscuits, candy, beverages, cheese, grocery products and convenient meals under the Cadbury, Jacobs, Kraft, LU, Maxwell House, Milka, Nabisco, Oreo, Oscar Mayer, Philadelphia, Tang and Trident brands in approximately 170 countries. The company had 2011 revenue of $54.4 billion. Kraft is the leading packaged goods company in Canada, tracing it roots to the vision of James Lewis Kraft of Stevensville, Ontario.
Difficult code reading challenge
The barbeque sauce product line at the Saint-Laurent plant produces 30 different stock keeping units (SKUs) at a rate of up to 265 bottles per minute. Ensuring that each individual package has the correct label is critical because some of the products have ingredients such as mustard and egg that may cause allergic reactions to certain customers. When the line is changed over to produce a different SKU number, the proper labels are manually loaded into the filling machine.
However, the possibility exists that the machine operator might load the wrong labels or that a few wrong labels might be accidentally mixed in with the correct labels. To address this concern, Kraft originally used laser-based barcode scanners to read the 1D barcode on each label as it passed by on the line and send the results to the programmable logic controller (PLC) that runs the machine. The PLC compared the code to the proper value and if the code was wrong the package was ejected from the line.
The problem with the laser scanners is that they are only capable of reading codes located within a small field of view. The label design is market driven so codes may be positioned at any location depending on the designer’s decision. As a result, when the labels are changed the code may be in a different position. This required that the position of the laser scanners be adjusted whenever the product line changed to a new SKU number, taking a considerable amount of the technical team’s time. Yet even when the laser scanners were positioned perfectly they still often failed to read the code.
The technical team was repeatedly called out to make adjustments to the 1D laser scanners and often struggled to determine why they generated no-read failures. “My team was frequently called upon to adjust the code readers,” Fortin said. “These calls made it difficult for us to fulfill other responsibilities. A considerable amount of time was also required on the part of the production team to inspect each of the packages that could not be read by the scanner to make sure it was correct.”
Move to image-based technology
The basic idea behind image-based technology is that the reader captures an image and uses a series of algorithms to process the image to make it easier to read. A typical algorithm searches the entire image for the code and identifies the position and orientation of the code for easy reading. Other algorithms handle degradations in code quality due to differences in material types and surfaces.
The DataMan 300 also provides built-in Ethernet which makes it easy to communicate with a PLC and the plant network.
Palmieri recommended the Cognex DataMan 300 image-based barcode reader because its 800 x 600 pixel image resolution provides a five inch by five inch field of view which is sufficient enough to capture an image of the entire label with the necessary resolution to easily read the code regardless of its position and in spite of degradation or print quality.
“The DataMan 300 also provides built-in Ethernet which makes it easy to communicate with a PLC and the plant network at a very affordable price,” Palmieri said.
The DataMan 300 uses the 1DMax® algorithm, which incorporates Hotbars® technology designed to handle difficult linear barcode-reading applications on high speed lines.
The 2DMax® algorithm is also an upgrade from existing technology, offering tremendous enhancements in handling damaged codes at high line rates and poorly marked or extremely damaged codes.
The DataMan 300 series offers the flexibility of integrated and controllable modular lighting and optics. The user can purchase just one model and choose the appropriate lens for their required working distance and field of view. The controllable, field changeable lighting modules allow the user to create the best possible lighting for their part, ensuring optimal read rates.
The DataMan 300 image-based barcode reader captures an image of the entire label with the necessary resolution to easily read the code regardless of its position and in spite of degradation or print quality
Near perfect code reading accuracy
Fortin started by replacing a laser scanner with a DataMan 300 barcode reader in one scan location on the barbeque sauce line. From the moment it was installed, the image-based reader virtually eliminated read failures, providing 99.9%+ read rates. Kraft made the decision to replace the three other barcode readers on the barbeque line with the DataMan 300. Four barcode readers are required on the line because it has four spurs. Since then the company has also replaced the laser scanners on three additional lines with the DataMan 300. Read performance has continued to be outstanding with 99.9%+ accuracy. No adjustment is required so the technical staff has been freed from the need to adjust the position of the reader during changeovers.
Fortin is able to do the installation and setup of the DataMan 300 code readers himself. He uses panand-tilt brackets that he buys with each code reader to mount the readers in place. He connects the reader to a personal computer and adjusts the light and focus on the camera. He connects the reader to a PLC via an Ethernet connection. The camera supports all popular PLC communications protocols. A photodetector in the inspection station provides a signal to the PLC that a bottle is in the station ready for inspection. The PLC instructs the barcode reader to capture an image and the barcode reader sends the code to the PLC. If the code does not match the product that is currently being run on the line, the PLC transfers the bottle to a reject conveyor. Fortin can install a DataMan camera in about two hours. “DataMan 300 barcode readers have significantly improved the efficiency of packaging lines at Kraft Foods Canada,”
Fortin concluded. “In the past our technical team had to spend a considerable amount of time adjusting laser scanners on various packaging lines. The production staff also had to spend time dealing with the many bottles with good labels that the laser scanners were not able to read. The new image-based barcode readers have solved these problems by providing near-perfect read rates. They are also economical to purchase and easy to install and maintain.”