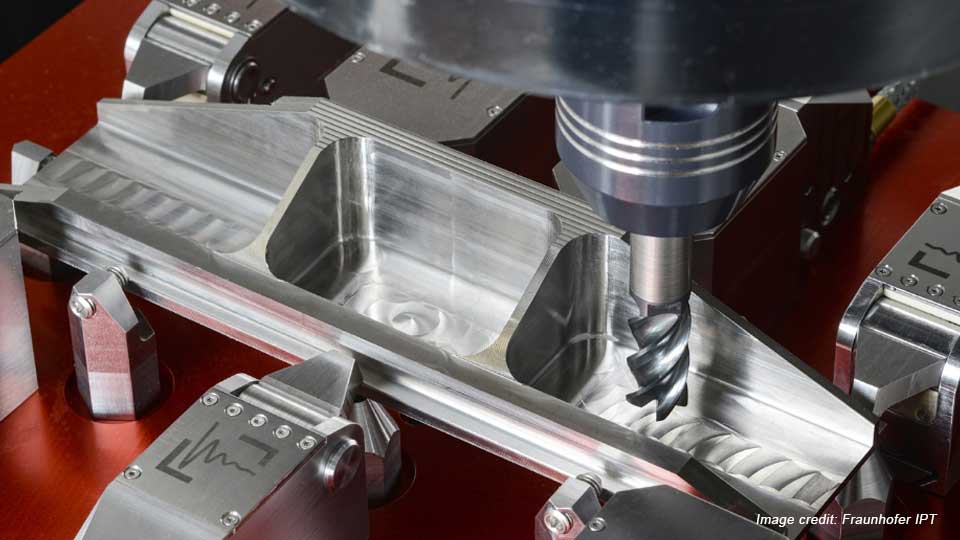
‘เยอรมัน’ พัฒนา ‘โซลูชันลดการบิดเบี้ยวของชิ้นส่วนระหว่างการกัด’
สถาบัน Fraunhofer IPT ร่วมกับพันธมิตร ประสบความสำเร็จในการพัฒนาโซลูชันเพื่อลดการบิดเบี้ยวของชิ้นส่วนที่เกิดจากความเค้นตกค้าง ด้วยการออกแบบกระบวนการตามแบบจำลองและระบบการจับยึดรูปแบบใหม่
Advertisement | |
การบิดเบี้ยวของชิ้นส่วนเป็นปัจจัยด้านต้นทุนที่สำคัญในการผลิตชิ้นส่วนโลหะ โดยเฉพาะอย่างยิ่งในกรณีของชิ้นงานขนาดใหญ่และผนังบาง ซึ่งมีบทบาทสำคัญในการออกแบบชิ้นส่วนน้ำหนักเบาหรือชิ้นส่วนอากาศยาน
ในระหว่างการผลิตและการอบชุบโลหะด้วยความร้อนจะตามมาด้วยความเค้นตกค้างที่ถูกสร้างขึ้น ซึ่งนำไปสู่การเบี่ยงเบนของรูปร่างและมิติของชิ้นงานระหว่างการตัดเฉือน โดยเฉพาะอย่างยิ่งเมื่อปลดชิ้นงานออกจากระบบจับยึด จะมีการบิดเบี้ยวของชิ้นส่วนอย่างมาก การบิดเบี้ยวของชิ้นส่วนในลักษณะนี้หมายความว่าไม่สามารถรักษาระดับความคลาดเคลื่อนในการผลิตไว้ได้ และชิ้นส่วนจะต้องถูกนำไปผลิตใหม่
คณะวิจัยจากสถาบัน Fraunhofer IPT ร่วมกับโครงการ VoKoES ได้พัฒนาแนวคิดที่ประกอบด้วยซอฟต์แวร์จำลอง (Simulation software) และระบบการจับยึด (Clamping system) รูปแบบใหม่ที่สามารถใช้ในการคาดการณ์และลดการบิดเบี้ยวของชิ้นส่วนระหว่างการกัดชิ้นงานที่ผ่านการรีดและอบชุบด้วยความร้อน โดยนำส่วนประกอบโครงสร้างการบินและอวกาศที่ทำจากไททาเนียมอัลลอย Ti‑6AI‑4V มาทดลอง ซึ่งโซลูชันที่พัฒนาขึ้นช่วยลดความผิดเพี้ยนได้ถึง 94 %
ด้วยเหตุนี้ นักวิจัยและพันธมิตร Access e.V. ได้เริ่มด้วยการตั้งโปรแกรมการจำลอง FEM ทางอุณหพลศาสตร์เพื่อกำหนดสถานะความเค้นตกค้างในช่องว่างที่ผ่านการอบด้วยความร้อน นอกจากนี้ ยังพัฒนาการจำลองการบิดเบือนเชิงตัวเลข ซึ่งช่วยให้สามารถคาดการณ์การบิดเบี้ยวของชิ้นส่วนหลังการกัดแต่ละครั้ง โดยการจำลองการบิดเบี้ยวของชิ้นส่วนจากความเค้นตกค้างนั้น นักวิจัยของ Fraunhofer IPT ได้ตั้งโปรแกรมการจำลองร่วมกับสถาบัน SLA (Institute for Structural Mechanics and Lightweight Design) ที่มหาวิทยาลัย RWTH ในเมือง Aachen ตามวิธี Finite Cell Method (FCM)
ทีมวิจัย Fraunhofer IPT ยังร่วมกับพันธมิตรบริษัท Module Works GmbH ประสบความสำเร็จในการรวมซอฟต์แวร์จำลองเข้ากับระบบ CAM เพื่อวางแผน Tool path จากการคาดการณ์ความผิดเพี้ยนของชิ้นส่วน ทีมงานได้ทดสอบวิธีการชดเชยต่าง ๆ เช่น การเปลี่ยนลำดับการตัดเฉือน หรือ ตำแหน่งของชิ้นส่วนเป้าหมายภายในพื้นที่ว่าง ผลลัพธ์ของการชดเชยจะแสดงให้เห็นผ่านระบบ CAM ซึ่งการรวมซอฟต์แวร์จำลองเข้ากับระบบ CAM มีข้อได้เปรียบตรงที่ไม่ต้องใช้ซอฟต์แวร์เพิ่มเติม ข้อดีอีกประการของกระบวนการนี้คือสามารถนำไปใช้กับกระบวนการตัดเฉือนชิ้นงานได้ทุกรูปทรงเรขาคณิต
นอกจากการใช้โซลูชันที่เป็นเทคโนโลยีดิจิทัลแล้ว บริษัท Innoclamp ซึ่งเป็นหนึ่งในพันธมิตรของโครงการนี้ ยังได้พัฒนาระบบจับยึดแบบไฮดรอลิกที่ปรับได้สำหรับจับยึดชิ้นส่วนระหว่างการกัด ด้วยระบบการจับยึดใหม่ทำให้ความเค้นตกค้างในชิ้นงานที่ถูกจับยึดสามารถถูกปลดปล่อยออกมาในลักษณะที่ควบคุมได้ในระหว่างการตัดเฉือน ชิ้นงานที่ปราศจากความเครียดจะถูกตัดเฉือนต่อไป ด้วยวิธีนี้สามารถสร้างรูปทรงตามต้องการได้โดยที่ชิ้นส่วนไม่บิดเบี้ยวหลังจากการคลายแคลมป์ และไม่จำเป็นต้องวัดชิ้นส่วนอีกครั้งในระหว่างขั้นตอนการตัดเฉือน
โซลูชันที่พัฒนาขึ้นประสบความสำเร็จในเฟสสุดท้ายของโครงการโดยใช้ตัวอย่างส่วนประกอบโครงสร้างการบินและอวกาศที่ทำจากไททาเนียมอัลลอยด์ Ti-6AI-4V ทั้งที่สถาบัน Fraunhofer IPT และบริษัท BoTech GmbH ซึ่งเป็นพันธมิตรโครงการ
คณะวิจัยมีแผนต่อยอดการใช้ซอฟต์แวร์ซิมูเลชันจำลองกลไกทางกายภาพ เช่น การโก่งตัวของชิ้นงานและเครื่องมือ ซึ่งเป็นการประยุกต์ใช้ Digital Twin สำหรับการทำนายการสั่นสะเทือนระหว่างการกลึงและหลังการตัดเฉือนของชิ้นส่วนที่ผลิตแบบเติมแต่งเนื้อวัสดุ หรือ AM (Additive manufacturing)
#เทคโนโลยกัดงาน #milling #digitaltwin #camsoftware #clampingsystem #Mreport #mreportth #ข่าวอุตสาหกรรม #onlinecontent
บทความยอดนิยม 10 อันดับ
- สรุปยอดขายรถยนต์ ครึ่งปีแรก 2022
- ภาพรวมอุตสาหกรรมโซลาร์เซลล์ของไทย
- สถานการณ์ชิปขาดตลาด 2022 จะสิ้นสุดเมื่อไหร่?
- 12 เทรนด์เทคโนโลยีมาแรงแห่งปี 2022
- 10 ตัวอย่างที่นำ 5G มาใช้งานได้อย่างน่าสนใจและประสบผลสำเร็จ
- เทคโนโลยีแห่ง G สู่ 5G เครือข่ายไร้สาย
- แบตเตอรี่ลิเธียมไอออนคืออะไร ตลาดจะก้าวไปในทางไหนในปี 2030?
- เทคโนโลยีสำหรับโลจิสติกส์ ทางเลือกสู่ทางรอด ปรับก่อนโดนเบียด
- นิยามใหม่ SME ใช้ “รายได้” เป็นตัวกำหนด
- FTA ไทย มีกี่ประเทศ พอหรือไม่ ทำไมต้องคิดเรื่อง CPTPP
อัปเดตข่าวทุกวันที่นี่ www.mreport.co.th
Line / Facebook / Twitter / YouTube @MreportTH