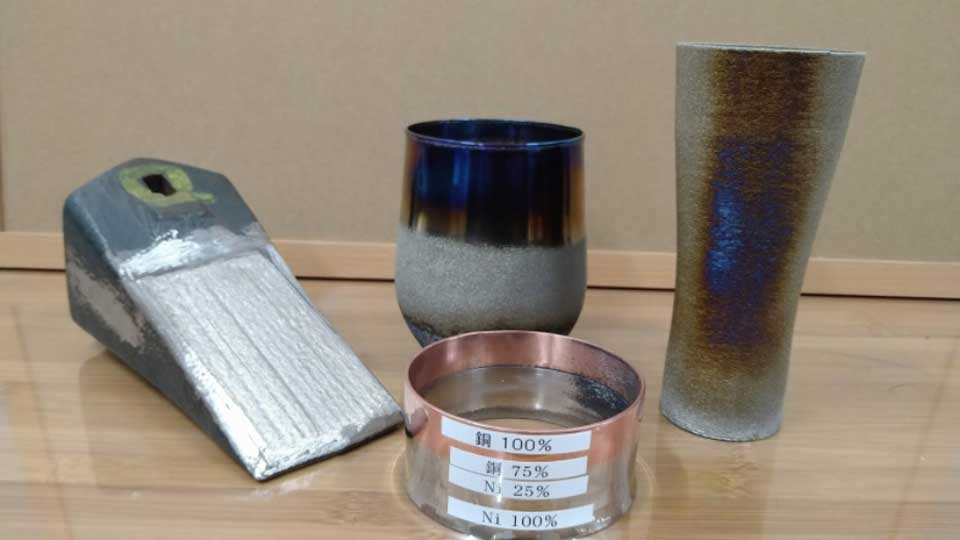
Additive Manufacturing is Passport that Japanese SMEs raise to Enter New Businesses
Although Japan has been lagging behind in the adoption of Additive Manufacturing (AM) technology compared to the West, nowadays, it is becoming in the spotlight, especially for SMEs in the metal processing-related industries, using it as a passport for entering new businesses.
Once Additive Manufacturing is passport that Japanese SMEs raise to enter new businesses
Ifuku Seimitsu, a manufacturer of precision parts is one of the companies that firmly choose Additive Manufacturing technology, a meeting room is always open for employees and experts in related fields such as 3D CAD to exchange ideas.
The meeting room at Ifuku Seimitsu is open up for experts can chat and share
In 2016, the company decided to acquire AM solutions from Sodick to install in the factory for entering into the 3D printing business. Ifuku Seimitsu currently installs three AM machines to produce products such as metal rice bowls, golf club heads and other metal parts manufacturing services. The company employs 50 people and more than 75% of them receive “3D CAD Engineer Certificate” and “3D Printer Engineer Certificate”
Mr. Motohiko Ifuku, president of Ifuku Seimitsu, expressed the company will thereafter dedicate research and development of materials technology, and collaborate with other companies to gear up AM technology more reliable and easy to use.
DAIMARU Steel Industry, an SME company whose main products are large metal parts for construction machinery, bridge parts, and other pump parts, are another company that uses Additive Manufacturing technology by choosing the DED AM System from Nidec, which Mr. Yoshihiko Ota, the managing director opinions on conventional manufacturing will no longer allow the company growing, therefore, AM technology must be used.
Workpieces of DAIMARU Steel Industry experimented to produce such as titanium alloy mugs.
Mr. Yoshihiko Ota explained that the company is currently trial printing aluminium to respond to orders from the construction of power plants, additionally, forming other prototype products such as cups made from titanium alloy which is difficult to produce by press machine. The knowledge gained from the production of these parts will be further applied to enable the company to step into the electric vehicle parts market.
KBV Research reported the market value of Additive Manufacturing which includes machinery, software and related services worldwide was valued at USD 3,529.80 million in 2021 and is expected to grow at a CAGR of 19.5% from 2022 to 2028. The benefits of AM technology are key drivers that reduce time spent on product development and production costs. While the metalworking industry is a great supporter of this technology as well.
How are machine manufacturers responding?
Many machine manufacturers see opportunities in the Additive Manufacturing market, they have dedicated more to the development of this technology. For example, OKUMA developed the MU-6300V LASER EX multitasking machine that supports a wide variety of materials printing. Their technology department said on its selling point that the technology can be used in a wider range of applications. For example to produce a die-casting mold from beryllium copper with high strength, good heat conduction, and mold surface made from High-Speed Steel (HSS) to obtain good heat resistance. The beryllium copper material is conducive to controlling the temperature of the processing mold, while the HSS is higher strength enabling mold more durable.
Mitsubishi Electric is another player intending to promote the AM market with the "AZ600" wire-laser metal 3D printer technology, that melts and laminates metal wires with laser. Using wire as a material has many advantages, such as lower material costs, easier storage and handling, and higher safety.
The Laser Manufacturing Technology Division revealed in terms of molding accuracy, it is not as accurate as powder materials, but it enables molding with fewer defects and improves quality and strength. Especially in terms of speed, the lamination volume can be increased by more than five times. Therefore, it can be used to print complex shapes such as propellers by printing near-net shape, which is quickly stacked in a rough shape and then finished by milling. It is said that the utilization efficiency of materials can be greatly improved compared to covering all manufacturing processes by cutting, and it will also lead to reducing environmental impact.
Compete in software development for high quality
AM is still a "new technology" compared to conventional cutting or called subtractive manufacturing. For that reason, it challenged users on setting up the optimal molding conditions for high-quality workpieces. Therefore, manufacturers are competing to develop software to ensure the quality of molded workpieces.
DMG MORI has developed software that is automatically configured according to the user's selected conditions such as hardness and tensile rigidity. It is expected to be commercialized around the beginning of 2024.
Nidec Machine Tool has improved the function to observe the lamination state with a camera and optimize AM, and will start providing it in April. By inputting the material, molding time, and shape data, then the molding conditions suitable are automatically set. President Haruhiko Niitani boasts it's an innovative function that uses artificial intelligence (AI) to set conditions.
In November 2019, Mitsubishi Corporation Technos opened a "Tokyo Customer Experience Center (Tokyo CEC)" showroom and AM technology research and development center. Currently, 3-4 companies come to visit each week and receive 12-13 print orders per month. Mr. Kazunari Hirose, General Manager of AMS said, “More customers recently have the theme of 'What happens if this workpiece is made by AM,' even if they do not have knowledge of AM, it is showing high interest in AM.”
One of the hurdles for the spread of AM in the future is the cost of equipment and materials. According to a leader of a major machine tools maker, because laser oscillators are used, the price is high.
Another manufacturer executive said, "Compared to the past, the application fields of AM have expanded dramatically," but predicted, "If the price of materials falls, AM will be used not only at production sites but also at home will increase." do.